Article
GET THE HEAT OUT
ARTICLE TAKEAWAYS:
- How to reduce die surface temperature to reduce porosity, shrinkage and scrap
- How thermal conductivity affects heat
Using High Thermal Conductivity Steel to Reduce Cycle time, Reduce Scrap, and Improve Part Quality
There are many benefits to increasing the cooling rate for an aluminum part in a die cast die. Reducing cycle time is an important cost savings. Improved part quality due to better cast structure of the aluminum, as well as reduced porosity is another. However, there is a limit to how many waterlines, and how close these water lines can be to the molding surface, before gross cracking of the die causes premature die failure in an H13 die. Tungsten alloy components have high thermal conductivity, but their high cost and low mechanical strength limit their practical applications.
Recently, two newly developed high thermal conductivity steels, Toolox44, SSAB Sweden, and DHA Thermo, Daido Steel, Japan have been solving more and more problems for die casters
By modifying chemistries, in particular lowering Silicon and Chrome, these two producers have come up with high thermal conductivity steels with sufficient mechanical properties to withstand the rigors of a die casting environment.
One of the first applications first time users (not yet believers) gravitate to, are shot blocks or sprue bushings. Exploding biscuits are no fun, therefore, decreasing their solidification time can eliminate blow-outs and reduce cycle time.
As shown in Figure 1, with both biscuits being measured by radiant thermograph after unclamping and just before lubricating, the biscuit off the Thermo sprue core was 120 C cooler in the same time frame. Figure 2 shows the improved cast structure of the aluminum in the biscuit off the Thermo as a result of the more rapid cooling.
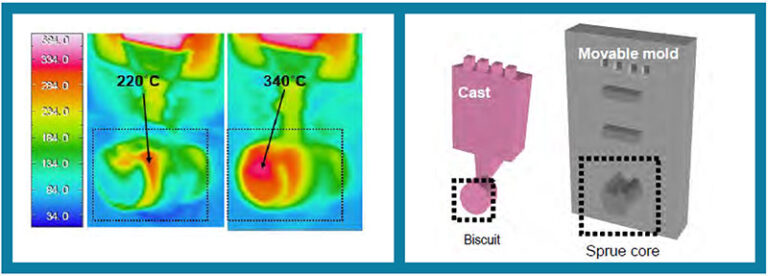
Figure 1
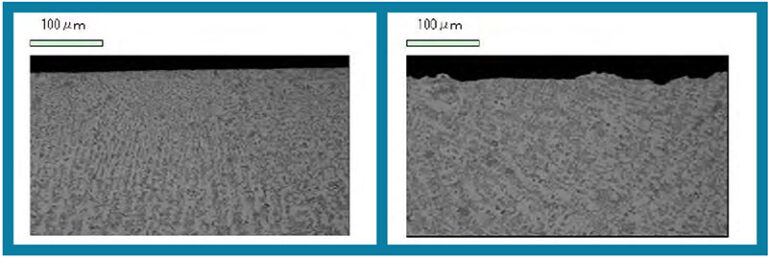
Figure 2
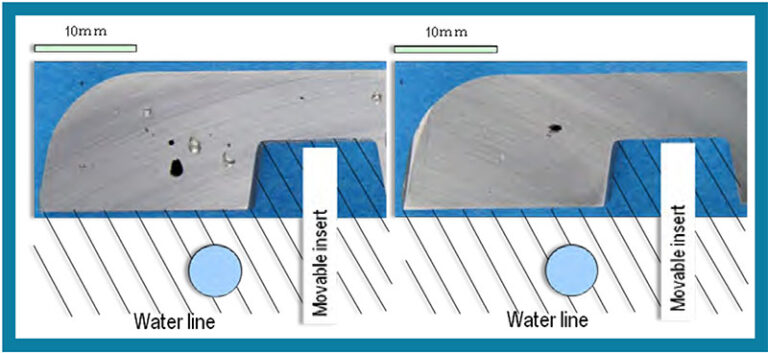
Figure 3
A die or insert made from one of the high thermal conductive steels will typically have an in-service surface temperature 50 C-to 90 C cooler than an H13 component with the same cooling. One benefit of the lower die temperature and improved heat transfer is reduced porosity. Figure 3 shows a typical comparison of the improved part quality due to reduced porosity.
Figure 4 is a piston for an Italian made motor scooter. The dies for these pistons were formerly made of Din 1.2343 ESR (H11). Switching to a high thermal conductivity steel yielded several benefits. First, they were able to shorten the die build time from 4 weeks to 3 weeks due to the elimination of the need to heat treat. Toolox 44 is supplied pre hardened to HRC45. Second, scrap rate due to porosity was substantially reduced. Third, the cast structure and mechanical properties of the piston were improved due to the more rapid solidification. An unanticipated benefit was that heat checking was slower to develop. It was quickly ascertained that this was due to the lower operating temperature of die surface, 50 C to 90 C cooler – there was a reduction of thermal stress.
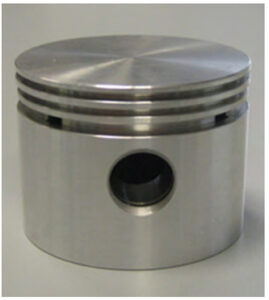
Figure 4
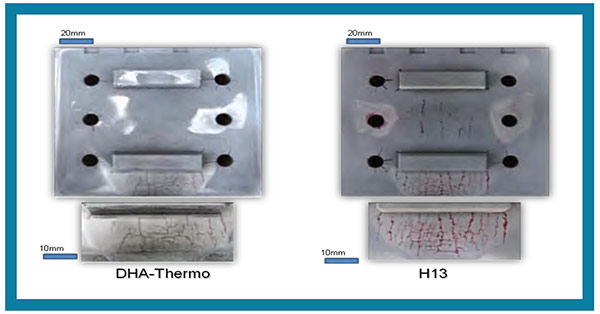
Figure 5
How Thermal Conductivity Affects Heat Checking Resistance
Thermal stress applied on die surface
σ = C x E x a x ΔT
C : Constant including Poisson ratio
E : Young’s modulus
a : Thermal expansion coefficient
ΔT: Temperature difference between
surface and inside
HIGHER THERMAL CONDUCTIVITY
= reduced ΔT
= reduced σ
Heat checking on moving die components as of 10,000 shots
Resolving Shrinkage Issues to Improve Yield Rates
Figure 6 is a motorcycle cylinder head cover. The original design called for two cooled core pins in the high lighted area. Insufficient cooling resulted in serious porosity due to shrinkage problem and a high scrap rate. A third H13 cooled core pin was added, but the high scrap rate due to shrinkage persisted. The H13 cooled pins were changed out for Thermo cooled core pins. The scrap rate due to shrinkage went to zero.
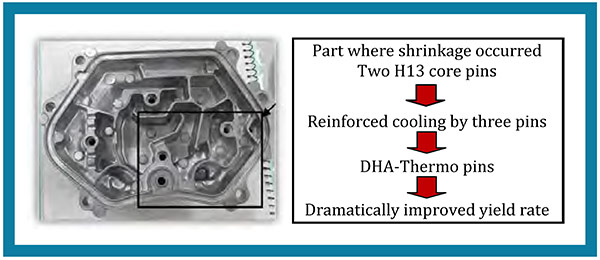
Figure 6
Soldering is another issue that can be improved by using a high thermal conductivity die material. Soldering is a chemical combination of the aluminum alloy and the iron in the die steel.
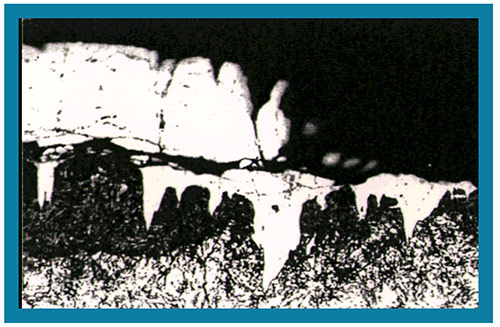
Figure 7
Lowering the surface temperature of the die, core pin, or insert that is soldering is one of the ways to improve the situation. Tungsten alloys have proven effective in lowering the surface temperature, but their high cost and low mechanical properties make them a last resort. The new, higher thermal conductive steels offer a new opportunity to reduce soldering issues. Using the same cooling as an H13 core pin or insert in a Toolox 44 or Thermo component will reduce the operating temperature of the surface of the component by 50 C minimum and help reduce instances of soldering.
By taking advantage of the high thermal conductivity steels, die casters are reducing scrap loss, improving the quality of the castings, and reducing cycle times.
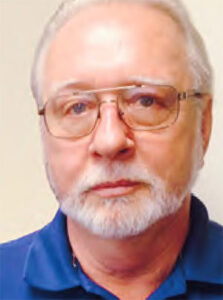
TOM SCHADE
Technical Sales
INTERNATIONAL MOLD STEEL, INC.