Article
Paul says there was a problem with a small progressive die that made a U-shaped bracket out of 2.4-mm-thick mild-carbon steel. One of the stages within the die kept breaking.
“It’s quite a thin construction across the die,” he says. “It was [similar to] a bridge piece, and it was cracking on both sides on the bridge. When it broke, it was increasing our downtime on the die. We tried all sorts of different tool steels, including D2 and A2.”
The company produces around 8,000 parts per run of this approximately 6-in. square part.
After reviewing the die’s construction, Paul felt it couldn’t be redesigned to make it last longer. Instead, he began a search for a different type of tool steel to increase its life and found one called Toolox 44 from International Mold Steel Inc., Florence, Ky.
Although he was reluctant to try the steel, Paul didn’t have much choice. “We used Toolox 44 as somewhat of a last attempt to repair the die and make it last longer/’ he says. “It was a success. With the A2 and D2 tool steels, we were getting probably 10,000 to 15,000 hits before the die broke. With the Toolox 44, we did 254,000 hits on the die insert.
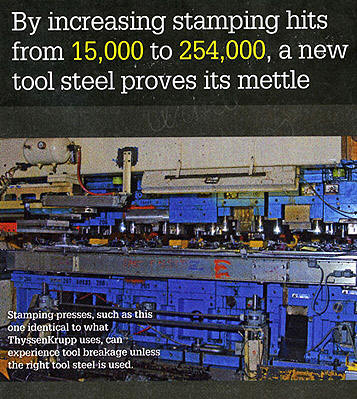
“We ran it for about 12 months, and there were a number of other issues with the die not involving the Toolox. The top punch was still D2 steel, and we had one instance where one of the other D2 steel punches broke and dropped across the die where the Toolox 44 is used. After the press came down on the broken punch, we found that the Toolox 44 insert was still in one piece. This incident could’ve caused a lot of damage to the tool, but it didn’t. We’ve been quite impressed with the steel.”
Paul says the company also tried quite a few other materials, and none stood up to the stamping until the company tried the Toolox 44.
“Although it’s a much tougher steel, it isn’t more difficult to machine,” he says. “But most of our dies are produced using EDM equipment.”
Along with the Toolox 44 steel, Paul says the company has also been trying different metal coatings on its dies to improve productivity. Titanium and a two-stage aluminum-carbonite coating will be used.
After the success of using Toolox 44 for this application, Paul says the company will be applying it in other projects. “It’ll be used in our progressive tooling because the die sections tend to be more complex with less support underneath rather than using it for tooling that produces larger stamped panels where we don’t have support problems,” he says. “We certainly won’t give it an easy process to continue our trials on either.”
Toolox 44 history
Toolox 44 was originally developed from Hardox 660 steel by SSAB Oxelösund AB, Oxelösund, Sweden. It’s a new quenched-and-tempered tool steel with high-impact resistance and low-residual stresses, giving it excellent dimensional stability. By using an intensive quenching process, the company’s able to reach the same hardness as regular tool steel with less carbon and fewer alloying elements. Through this process, Toolox 44 has fewer carbide inclusions, making it easier to machine.
Because it’s already at 45 HRC, heat treating isn’t needed after machining, and it can easily be machined with either carbide or high-speed-steel cutting tools. It’s well-suited for stamping applications, for which it offers excellent impact toughness and long service life, according to Tom Schade, executive vice president of International Mold Steel.
Another area in which Toolox 44 has increased productivity is blanking dies. In one application, nitride-coated Toolox 44 was used for a blanking die and blanked a 3.8-mm-thick mild-carbon steel sheet. Before Toolox was used, the company tried a D2 tool steel for the die at 58 to 62 HRC, which gave it 10,000 hits before breaking. The company then tried a D2 tool steel at 54 to 56 HRC, which gave it 10,000 hits before breaking. Next, the company tried a DC 5 3 tool steel with 8 percent chromium, which gave it 15,000 hits before breaking. After failing with these tool steels, the company tried the Toolox 44 with a nitride coating on the surface. It’s given the company more than 254,000 hits and remains in operation.
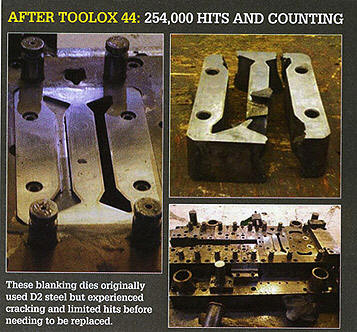